최근 완성차 업계에서는 브랜드 충성도가 중요해지고 있다. 시장의 양적 성장이 둔화되면서 브랜드 재구매율 관리가 중요시됐고 이 때문에 고객들의 감성적인 부분까지 충족시켜주는 브랜드 충성도를 높일 필요성이 생긴 것이다.
지난해 기준으로 전 세계에 운행되고 있는 현대·기아차는 5천만 대에 육박하면서 현대·기아차는 브랜드 이미지 강화를 통한 충성도 향상을 꾀하고 있다.
특히 원활한 AS부품 공급과 빠른 수리는 브랜드 충성도를 높여주는 가장 큰 요소 중에 하나로 현대모비스(대표 정명철)는 현대·기아차를 타는 운전자들이 안심하고 차량을 몰 수 있도록 최대한 빠르게 순정부품을 공급하고 있다.
순정부품이란 생산 및 설계단계에서부터 차량이 최적상태로 운행될 수 있도록 제작된 부품으로 신차 생산 시 공급되는 부품과 동일한 부품으로 볼 수 있다. 자동차는 2만여 개의 부품이 유기적으로 맞물려 운행하기 때문에 고장 시 순정부품 교환이 안전하다.
◆ 전 세계 어디에서나 빠르게 순정부품 받아볼 수 있도록 첨단 시스템 운영
현대모비스는 현대·기아차의 순정부품 책임공급자로서 운전자들이 이들 순정부품을 빠르게 받아볼 수 있도록 하기 위해 전 세계 각지에 물류 망을 구축하고 첨단 시스템으로 이를 관리 및 운영하고 있다.
현대모비스는 국내에 4개의 대형 물류센터를 두고 이곳에서 권역별 물동량을 중앙집하한 후 일괄분류작업을 거쳐 전국 23개 부품사업장과 43개 정비파트로 순정부품을 공급하고 있다. 해외에도 52개의 직영부품창고를 두고 있다.
현대모비스는 막대한 투자비용과 유지 및 보수비용이 들어가는 이들 직영부품 거점들을 구축하고 국내 1천600여 개 대리점과 해외 1만1천300개 딜러에 부품을 공급한다. 수도권 및 대도시는 물론 산간도서지역에서의 수급도 어려움이 없도록 하고 있다.
또한 AS부품의 정확하고 신속한 공급을 위해 첨단물류시스템을 구축해 운영 중이다.
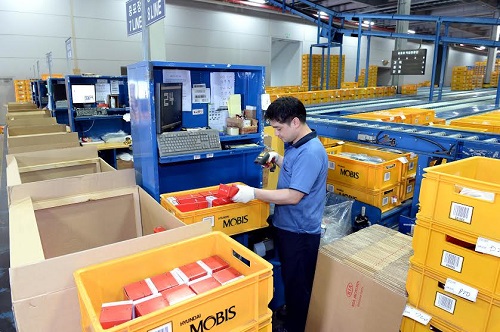
현대모비스는 양산 차종 93개와 단산차종 120개 총 213개 차종에 부품을 공급하고 있으며 부품 품목 수는 무려 214만 품목에 달한다. 단산 차종의 품목은 전체의 약 56%로 단산 차종 부품 재고량만 해도 약 2천억 원에 이른다.
이중에서도 단산경과가 오래된 차종의 재고는 약 450억 원 수준으로 이는 전체 보유재고의 약 13%에 해당하는 규모다. 이렇게 많은 단산품목을 보관하기 위해 현대모비스는 전용창고를 따로 운영하고 있다.
◆ 국내 최대 규모 및 시설을 자랑하는 현대모비스 아산 물류센터
충남 아산 인근 24만1,402㎡(7만3천24평) 부지에 위치한 국내 최대 규모를 자랑하는 아산물류센터는 현대모비스의 4개 물류센터 가운데 가장 큰 규모와 최신 설비를 갖췄다. 이곳에서는 현대·기아차 국내 보수용 부품을 70개 사업소에 공급하고 해외 201개 국가에 기아차의 AS 보수용 부품을 공급하고 있다.
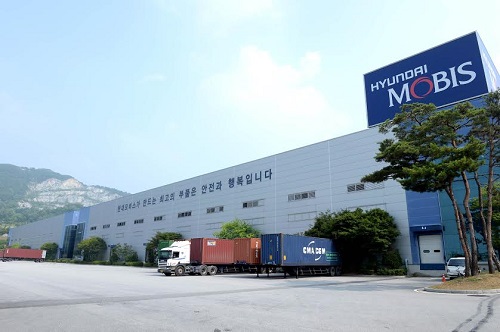
아산 물류센터는 PDA를 활용한 물류처리 시스템을 도입해 물류 창고내 부품의 저장, 출고를 비롯한 전체 작업 공정에 대해 실시간 공정처리와 실물과의 정보 일치화를 이루고 있다. PDA로 부품 바코드를 찍으면 수량 및 저장 위치 등 다양한 정보를 알 수 있다.
이 시스템을 도입하면서 별도의 숙련 없이 초보자도 쉽게 작업할 수 있게 됐으며 생산성도 30% 이상 향상됐다. 또한 물품 배송과 함께 재고관리가 동시에 진행되다보니 로스율 역시 기존보다 낮아졌다.
이렇게 불출된 부품은 컨베이어 시스템을 통해 포장 공정으로 옮겨진다. 물론 부품이 담긴 플라스틱 바구니에도 바코드가 부착돼 있어 어떤 부품이 어디로 배송되는지 바로 알 수 있다. 포장 작업자는 역시 이 바코드를 읽고 특별 제작된 종이 박스에 담아 주문지역으로 배송한다.
물류센터의 바닥은 강섬유강화 콘크리트(SFRC)로 시공됐다. SFRC는 콘크리드와 강섬유를 혼합한 복합재료로 보통의 콘크리트에 비해 10배 이상 충격에 강하다.
무거운 부품을 운반하는데다 선반과 선반사이 공간이 없기 때문에 자칫 바닥이 평평하지 않으면 안전사고로 이어질 확률이 높고 특히 마무리 작업은 레이저를 이용해 바닥을 오차없이 평평하게 해 주기 때문에 중장비를 이용한 물류 운반에 큰 도움을 주고 있다.
[소비자가만드는신문 = 김건우 기자]